Zeke Reichert's
Digital Portfolio
2015 Wagner Subaru Internship
Click the picture to download the report
Document Description
This document is a business/technical writing piece that was used to explore future career options. This document needed at least 2 potential careers with internships that apply to each. Also included in this report was a list or resources used while researching, these sources were recorded in APA style citations. The careers explored in this document were automotive service technician and veterinarian. The potential internships found were at 3 locations, Wagner Subaru, Grismer automotive service, and Hosket veterinarian services. These are places that relate to the potential careers listed and give experience in those fields. Lastly section based on the research process was completed, this gave an overview of how this document was created.
When I first arrived at Wagner Subaru I had almost no experience dealing with and working on Subaru’s or working with customers to work on and sell cars/parts. I had never been in an automotive environment like this where everything had a time that it needed to be done and the number of mistakes made was extremely minimal. The feeling was scary, especially because I had never been under any kind of pressure like that where I needed to get a job accomplished within a certain time and at a certain spec.
​
I found this way of working to be very difficult, as I take my time with most everything I do when working on anything whether it be an engine or setting up for a recall. The way that I was able to work through this was through these two things: #1 experience in these environments for an extended period of time to adapt to the environment #2 learning how to do the jobs with better success rates and quicker time rates. Once I had been exposed to the environment for long enough the jobs felt fairly natural, I was constantly learning about new things. In the first week alone I learned the whole express service system and the S.A.S.S system. What this process does is optimize how the express oil change and tire rotation services work by incorporating steps and teamwork to speed it along.
​
The biggest project I was assigned in my internship was a personal one that the technicians at the dealership helped me with, which was rebuilding the engine in my own car. From the day I arrived at the dealership they had told me that it needed to get new head gaskets because of its age and that this would be a really strong takeaway for an intern position. To start the process after the service bays were closed for the night we brought my car in and started to pull it apart bit by bit to take the motor out. By the end of the evening around 7 PM, my engine was out and on a stand where it was more accessible. The next day the master techs showed me how to take apart the engine, and showed me a few tricks to make it so that I wouldn’t have to stress as much when I had to put it back together. After pulling the engine apart and taking out the bad head gaskets I was taught how to clean all of the parts of the engine and fixed it.
Internship Reflection



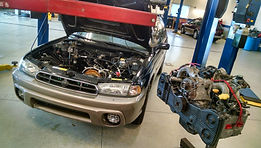

Day 1: Here's where I learned the ropes. Today I was brought to both of the dealerships and learned what the difference between them was and I got to see the different sections of them. Relatively simple, but nice learning about the dealership.
​
Day 2: This was one of the most interesting days of the internship, I went to the new dealership and got to work in the service drive with the other mechanics. The mechanics told me what each of them did and what parts of the car they focused on. The most interesting one I can think of was “short block resealing”. There is a recall out for a lot of Subaru’s because they leak oil heavily, the fix? Pull the engine completely out and put new seals into it. I watched as a master tech pulled the engine out and put it back in in one day!
​
Day 3: I went to the old dealership today and ran some deliveries for the new dealership. While I was visiting the old dealership I learned all about recalls. I saw that recalls are one of the most important service jobs at the dealership as this is where most of the customer satisfaction ratings come from.
​
Day 4: On day 4 I was given the assignment to PDI (Pre Distribution Inspection) a car. To PDI a car is to get it 100% ready to sell and for the customer to come get it. There is a full checklist of things that need to be done to PDI a vehicle including: Filling up the gas, checking tire pressure, removing protective plastics, washing and waxing, topping off all fluids and more! It was very time consuming and not my favorite task.
​
Day 5: Here I was given the Express Tech run-down. The task of the Express Tech is to manage the Express bay, the express bay is where cars come to get their oil changed and tires rotated in about 15 minutes! This job was a lot more up my alley it was dirty, but a lot of fun getting to see the underside of so many cars and each unique problem that surfaced when we did the Multi-Point Inspections!
​
Days 6: Now I was given the placement of a Parts manager, boring name but the job is much more difficult than you might think! You need to write down everything that is sold, returned, recalled and re-stocked! It is all managed by a computer system so all we had to do was organize. But some of these parts can get quite large and hard to store, to solve this problem I used the largest boxes we were supplied to house the smaller boxes freeing up the shelves for heavier items.
​
Day 7: This was a tough day for me because it started off with my car not even making it to the dealership! I was on my way and the Head-Gaskets (A common failure point on Subaru vehicles) blew out causing my car to overheat leaving me stranded. Wayne Wilson came and got my car and we took it back to the dealership. This is where Wayne gave me my final assignment for the final 3 days. To remove my engine, install new head gaskets and put it back in. The shop can do these in a matter of hours, yet 3 days seemed daunting to me. That evening after hours at the dealership we set to work pulling the motor out, a task that with the help of the Wagner team only took a few hours. The engine was set on a stand and left for tomorrow.
​
Day 8: Today I took my engine off the stand and started disassembly, Wayne, Paul and Denton helped me through this guiding me on how to correctly disassemble the intake, valves and most importantly the heads. here I get to see what a new head gasket looked like compared to the old. It was covered in a thin black sealant and it had no rust anywhere whereas my old ones were covered in rust, had no sealant left and had visible places where they had blown. Assembly was as simple as disassembly, it was just like putting together a puzzle! once the motor was put back together we set it on the stand and waited until tomorrow.
​
Day 9: This was the day that my engine would be going back into my car! I was very excited as this was going exactly to plan! I was called in after work and we pushed my car into the service bay where they then pulled up chairs and sat down. This was a test for me... They told me that I should be able to get the engine in all by myself. I was going great into I hit my first roadblock I did not know how to align the engine and the transmission, they told me that there was a set of splines I needed to look for and as soon as I rotated the engine to line up with the splines it slide right in! bolted everything down and attempted its first start, everything sounded healthy. I took it on a short drive around the block where it overheated again! It turns out Subaru's are very picky and will overheat if there is any air in the system, so before everyone left we bled my coolant system one more time bringing the temperature right where it needed to be. I then drove home to no problems.
​
Day 10: This was my last day of the internship and possibly the best! The day started off great when a customer brought us breakfast because she likes our service so much! Once I had a hearty meal I was ready to tackle the line of cars that were in need of oil changes, tire changes and more. I hovered around the bays waiting to people needing a hand which ended up being a very interesting and useful job. I was called to the front of the building which surprised me, but it turns out they were taking my picture for the website! I am on the Wagner Subaru website! That was very exciting for me and it was a great way to conclude my internship experience as a service technician and Lot Tech at Wagner.
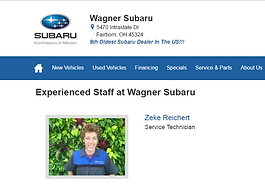
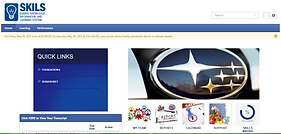


